Clean Technology
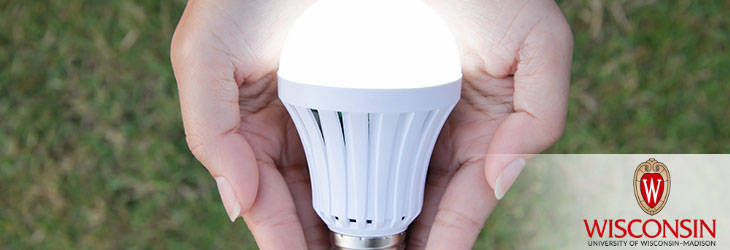
Method to Produce Furandicarboxylic Acid (FDCA) from 5-Hydroxymethylfurfural (HMF)
WARF: P160074US01
Inventors: James Dumesic, Ali Hussain Motagamwala
The Wisconsin Alumni Research Foundation (WARF) is seeking commercial partners interested in developing a scalable method to upgrade biomass-derived 5-hydroxymethylfurfural (HMF) to the value-added chemical 2,5-furandicarboxylic acid (FDCA) and then easily separate the FDCA from the solution.
Overview
The platform molecule HMF is derived from biomass and converted into a variety of downstream products. One of the most important of these is FDCA, which is used as a monomer in the production of fiber and packaging polyester (PEF) that competes with the petrochemical PET. Given its high value potential, FDCA has been classified by the Department of Energy as one of 12 priority chemicals for establishing a sustainable chemical industry of the future.
To date, research on HMF has focused on maximizing HMF yield from carbohydrates, while upgrading, separations and the economics of the process remain less explored but important problems. Current methods to produce HMF from biomass-derived sugars exhibit either low selectivity (40 to 70 percent with Dutch company Avantium’s process) or difficult product separation. A new method that integrates high conversion and easy separation would be of significant commercial advantage.
To date, research on HMF has focused on maximizing HMF yield from carbohydrates, while upgrading, separations and the economics of the process remain less explored but important problems. Current methods to produce HMF from biomass-derived sugars exhibit either low selectivity (40 to 70 percent with Dutch company Avantium’s process) or difficult product separation. A new method that integrates high conversion and easy separation would be of significant commercial advantage.
The Invention
UW–Madison researchers have developed a process for oxidizing HMF to FDCA in quantitative yields, with or without separating the HMF from the reaction solution. For maximum sustainability, the HMF can be obtained from the dehydration of biomass-derived sugars in the organic solvent gamma-valerolactone (GVL). The HMF is oxidized to FDCA in situ with an agent such as molecular oxygen over a supported metal catalyst. The FDCA is easily extracted from the reaction mixture by adding a relatively inexpensive aromatic solvent such as toluene.
The use of aromatic solvent results in a two-phase system in which the first phase is rich in GVL and the second phase is rich in FDCA. In this process, more than 90 percent of the FDCA is recovered in the aqueous phase. Moreover, the GVL can easily be separated via distillation given the large difference in the boiling points of GVL and toluene.
The use of aromatic solvent results in a two-phase system in which the first phase is rich in GVL and the second phase is rich in FDCA. In this process, more than 90 percent of the FDCA is recovered in the aqueous phase. Moreover, the GVL can easily be separated via distillation given the large difference in the boiling points of GVL and toluene.
Applications
- Upgrading HMF to the high value chemical FDCA, which could replace petroleum-based terephthalic acid in the production of polymers used in packaging, bottles and more
Key Benefits
- Economically viable process
- Reduces costs associated with HMF separation
Stage of Development
The new method has been shown to convert HMF to FDCA in quantitative yields, followed by easy separation of FDCA using a relatively inexpensive solvent.
For current licensing status, please contact Jennifer Gottwald at [javascript protected email address] or 608-960-9854